One of the many tools that condition monitoring enables us to provide is predictive maintenance. Predictive maintenance allows you to improve business efficiency by minimizing downtime and increasing productivity. This is achieved by strategically monitoring assets and conditions specific to your business, which vary significantly based on your industry. While several companies directly benefit from predictive maintenance, it is crucial to know the applications you wish to automate to understand which type of technology best suits your business need. Brewer Science leverages 40 years of extensive experience to provide customers with customized solutions specific to their unique business needs. Our customers are in remarkably diverse markets, which allows us to tap into our materials expertise with an extensive array of products—some on the market and others developed ourselves through our Smart Devices and Printed Electronics Foundry. We have identified six examples of predictive maintenance to illustrate the diverse capabilities it can have on your business operations.
1. Refrigeration Sensor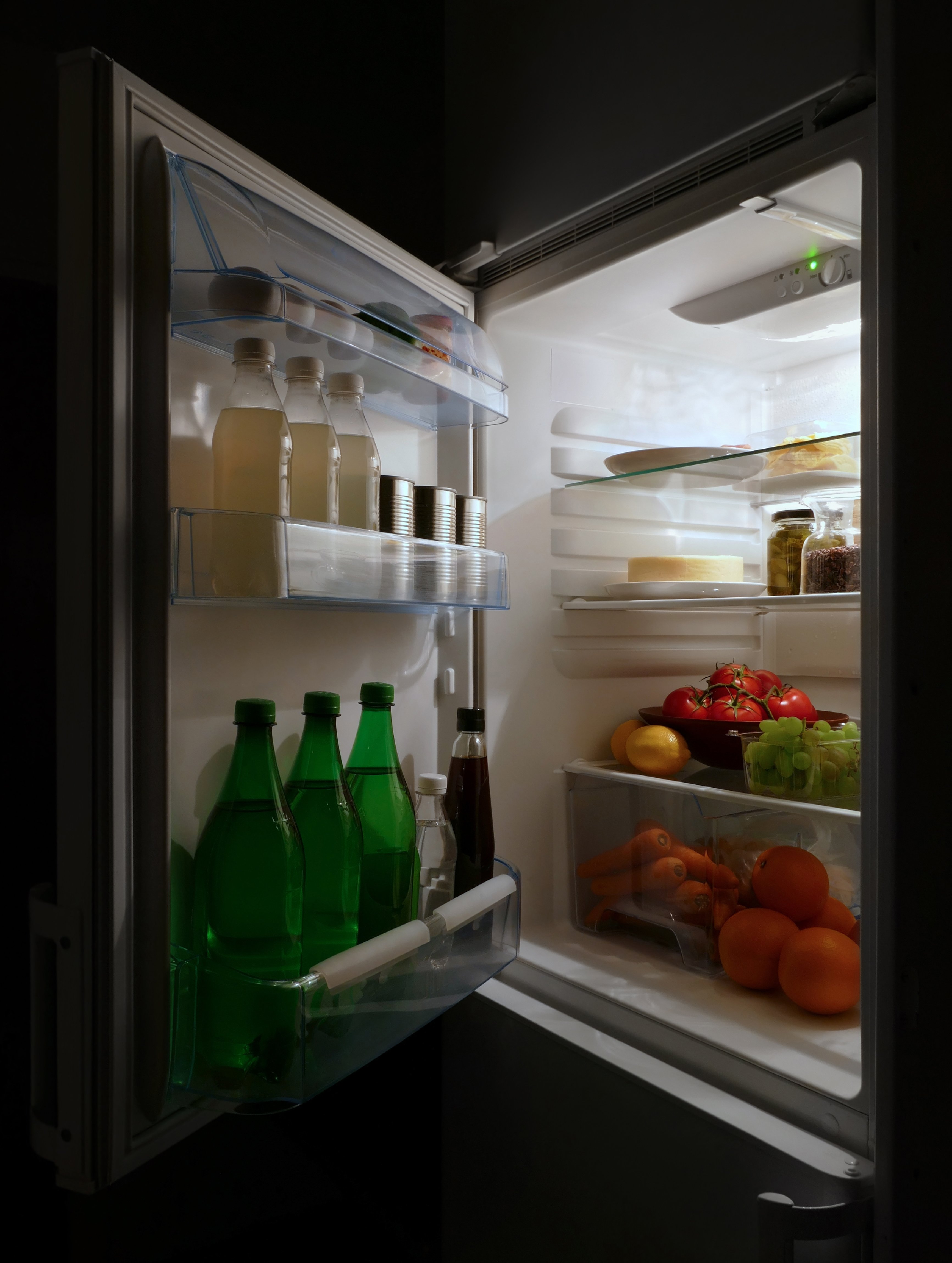
In a restaurant, the health of any food storage or cooking utility is paramount to the business’s success. If a restaurant’s refrigerator was beginning to malfunction or require any type of update, predictive maintenance technology could measure the functionality and alert restaurant staff to any issues. A sensor would evaluate elements of the fridge such as temperature and vibration to determine asset performance. This advance notice would enable the restaurant to fix the potential problem before it results in downtime, loss of goods, or most importantly, customer safety. This is just one of many examples of when to use temperature sensor arrays for FHE applications.
2. Power Outage Prevention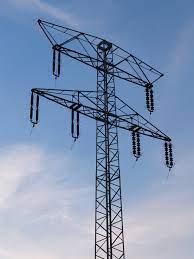
Power outages can cause significant inconveniences for those they affect—and can be life-threatening in situations such as hospitals or assisted living facilities. With predictive maintenance technology, they can be detected early and therefore mitigated. Sensors provide insight into assets using artificial intelligence and cloud-based computing. This intelligence informs companies within the energy industry when equipment is likely to fail. One of the many facets that make Brewer Science’s Smart Devices and Printed Electronics Foundry highly competitive is that our systems provide actionable insights, presenting data in a way that allows you to understand what needs to happen to avoid the unforeseen maintenance, or in this example, a power outage.
3. Oil and Gas Industry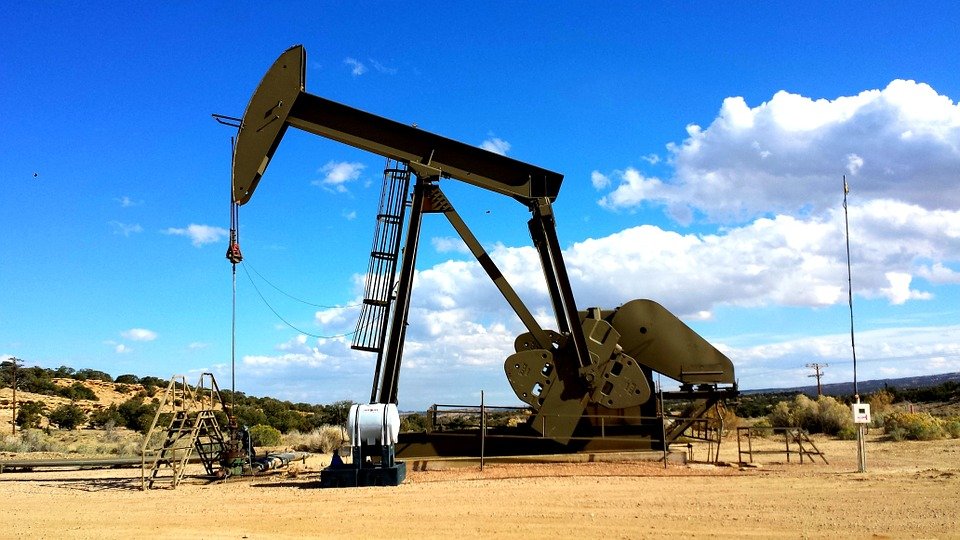
The oil and gas industry often lacks visibility into the condition of their equipment in remote offshore places. Maintenance technicians would visit these sites based on a time interval to inspect the condition of the equipment even when it is not necessary. As we learned with the Deepwater Horizon Oil Spill of 2010, routine inspections can sometimes neglect to evaluate essential valves or sensors. Through predictive maintenance, oil and gas companies can assess the health and performance of their equipment and only schedule maintenance when an issue that is out of the norm is detected. Strategically placing sensors on valves and activating sensors during certain industrial conditions allows maintenance workers to track malfunctions effectively and efficiently.
4. Building Management
By using environmental monitoring, you can control and monitor buildings from any location using predictive maintenance technology—specifically, software for ventilation and energy management. This also enables owners and managers to keep the building environment within a specific temperature range and track humidity or moisture by using sensors specific to the desired outcome. The sensors transmit the information to a cloud-based computing data analyzing software that allows you to detect abnormalities or changes over time so you can schedule maintenance when needed. This type of monitoring can help improve overall energy costs for the building.
5. Manufacturing Monitoring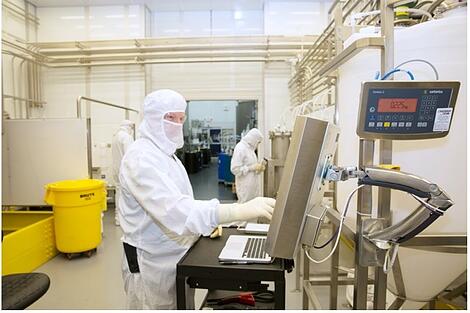
Since a manufacturing plant tends to have many costly assets and valuable equipment, they might invest in infrared imagers to monitor aspects of assets, such as temperature, to prevent overheating. This predictive maintenance system helps plants avoid overusing essential equipment, pushing machinery to the point of disruptive breakdowns.
6. Aircraft maintenance
If an airplane has an unexpected breakdown, it can lead to delays, incur considerable costs, or worse. Usually, aircraft maintenance relies on preventive maintenance, such as a set schedule for inspections and repairs. However, using predictive maintenance that uses sensors and flight data recorders can predict where irregularities may occur and schedule planned maintenance ahead of time. Helicopter maintenance includes Health and Usage Monitoring Systems (HUMS), which are sensors and embedded diagnostic software that monitor and communicate the health and maintenance needs of critical components by detecting abnormalities in the vibration of sensors.
Brewer Science’s diverse experience brings innovative solutions to customers’ unique business needs. No matter the industry or the application, a talented team of engineers brings together material expertise and innovative creativity to help you achieve your business objective. Monitoring machinery functions, industrial functions, the temperature of machines or the environment, the moisture or water content, or even valve vibration can ensure you do not miss essential productivity concerns and lose productivity due to downtime. To learn more about Brewer Science’s Flexible Hybrid Electronics Foundry and how you can use it to implement predictive maintenance in your business, talk to an expert today.